Чорна металургія
Чорна металургія – галузь важкої промисловості з виробництва чавуну, сталі, прокату, феросплавів, а також сталевих і чавунних виробів.
Схема організації металургійних виробництв.
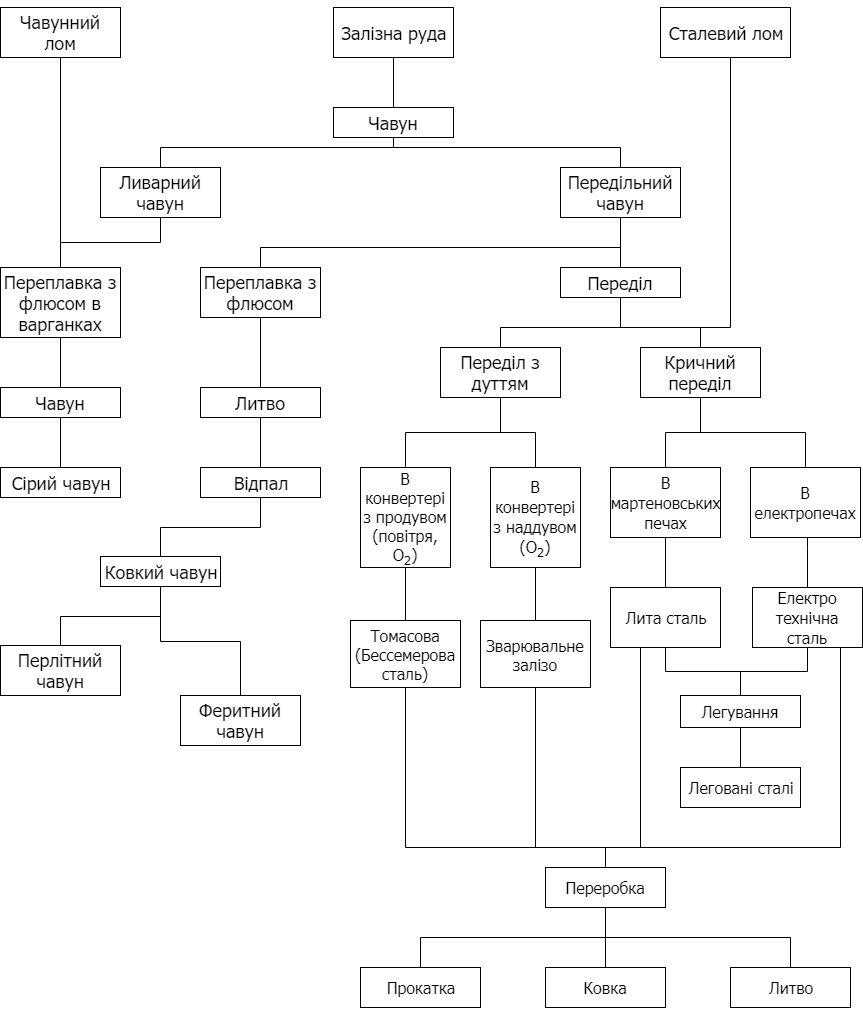
Виробництво чавуну
Підготовка руди складається наступних процесів:
- Збагачення основною речовиною сухим, мокрим або магнітним способом;
- Перетворення неоксидних руд методом випалювання в оксиди, наприклад, для піриту FeS2 і сидериту FeCO3:
4FeS2 + 11O2 = 2Fe2O3 + 8SO2
6FeCO3 + O2 = 2(FeIIFeIII2)O4 + 6CO2
- Створення необхідного гранулометричного складу шляхом подрібнення або брикетування.
Способи виплавки чавуну:
- доменний процес (отримання всіх видів чавуну);
- процес в обертових трубчастих печах (одержання тільки передільного чавуну).
Доменний процес складається з наступних стадій:
- Протиток – тверда шихта просувається по доменної печі зверху вниз, а гази, навпаки, знизу вгору;
- Утворення карбон(II) оксиду – гаряче повітря ( “гаряче дуття”) при 800*С, одержане в доменних нагрівачах (каупер), збагачується киснем і через фурми продувається в домну, в цьому повітрі відбувається неповне згоряння коксу (оскільки кокс беруть в надлишку) з утворенням CO, який піднімається вгору;
- Відновлення залізної руди – відбувається під дією CO (непряме відновлення) і дрібно змеленого коксу (пряме відновлення), при цьому утворюється тверде губчасте залізо;
- Регенерація карбон(II) оксиду – CO2, що утворився при відновленні залізної руди, перетворюється коксом знову в CO, який повертається на стадію відновлення залізної руди;
- Коксування заліза – губчасте залізо каталізує процес встановлення рівноваги (рівновага Будуара):
2CO ⇄ CO2 + C
дрібнодисперсне вугілля проникає в сплав і знижує температуру плавлення заліза до 1150*С, тобто приблизно на 400*C;
- Розплавлювання і спуск чавуну – при температурі вище 1150*С сплав феруму з карбоном плавиться, розплав збирається в прийомнику металу (горн), звідки періодично (кожні 4-6 годин) здійснюється його спуск;
7. Утворення і спуск шлаку – шлак утворюється в розплавленій зоні з присутніх в руді домішок і флюсів, останні переводять тугоплавкі компоненти руди в легкоплавкий шлак. До кислих руд (багаті SiO2) додають основні флюси (CaCO3), а до основних руд (багаті CaCO3) додають кислі флюси (SiO2). Порода з флюсами і глиною утворює шлак, що складається з кальцій алюмосилікатів. Шлаки збираються на поверхні розплаву чавуну, спуск шлаку здійснюють або періодично, або безперервно.
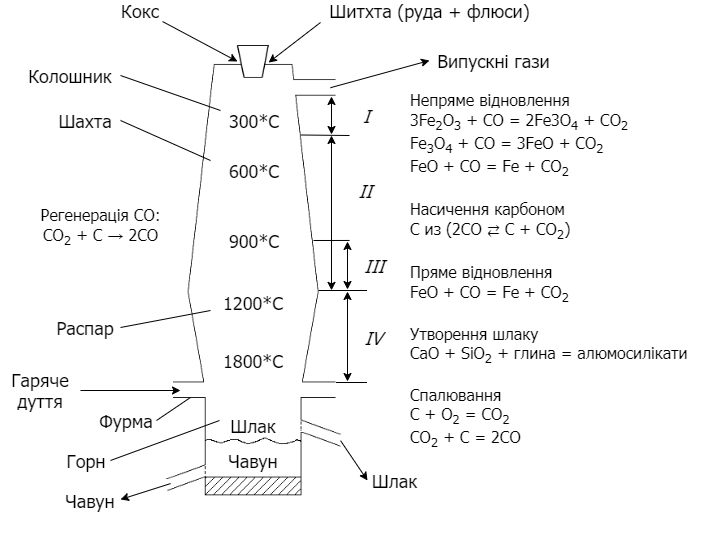
Принципова схема доменної печі і процеси, що протікають при виплавці чавуну. I – зона попереднього підігріву; II – зона відновлення; III – зона насичення карбоном; IV – зона плавлення.
Продукти доменного процесу:
- чавун, що містить, крім Fe, 3-5% C, 0,3 – 2,5% Si, 0,5 – 6,0% Mn, 0,08 – 2,2% P і 0,03 – 0,12 % S;
- доменний шлак, що складається з кальцій алюмосилікатів. Використовують для приготування щебеню, гравію, шлакобетону, термозіту (шлаковая пемза), пінобетону, шлаковати (для термоізоляції), швидко охолоджений і перемелений шлак йде на отримання доменного портландцементу;
- доменний газ, що містить 60% N2, 30% CO, 10% CO2 і багато пилу. Після видалення пилу цей газ використовують для підігріву повітря, для вироблення електроенергії (на ТЕЦ) і як горючий газ.
Процес отримання чавуну в обертових трубчастих печах полягає в змішуванні подрібненої руди з вугільним пилом і нагріванні цієї суміші шляхом спалювання частини вугільного пилу. У цьому процесі утворюються збіднені за вмістом карбону гранули чавуну, які переробляють в сталь.
Випал чавуну – термічна обробка сирого чавуну з метою поліпшення ковкості, в результаті отримують ковкий перлітний чавун і ковкий феритний чавун.
Щоб отримати перлітний чавун, сирий чавун розливають у форми, отримані злитки ущільнюють сумішшю Fe2O3 і (FeIIFeIII2)O4 протягом п’яти-шести днів витримують при 950 – 1000*С, при цьому поверхня злитка позбувається карбону і чавун стає схожим за ковкістю на сталь. Його застосовують для виготовлення невеликих предметів (ключів, деталей замків, важелів, ланок ланцюгів, гайок і т.п.).
Щоб отримати феритний чавун, проводять випал сирого чавуну, покритого шаром піску і шлаку, протягом трьох-чотирьох днів, при цьому надлишковий карбон виділяється з чавуну у вигляді графіту і чавун стає ковким.
Виробництво сталі
Конвертерний і мартенівський процеси (бессемерівська плавка і томасівська плавка).
Перетворення чавуну в сталь засноване на видаленні з чавуну S, P і Si, а також зниженні вмісту карбону за допомогою окиснення.
Спосіб переділу чавуну в конвертері був відкритий в 1854 році (Бессемер, Англія). Цей сіособ придатний тільки для переділу чавунів, бідних на фосфор. Переділ чавунів зі значним вмістом фосфору став можливим тільки після розробки в 1878 році (Томас, Англія) процесу з використанням конвертера з футеровкою матеріалами, які мають основні властивості.
Конвертерний процес.
Переділ чавуну проводять в спеціальному апараті – конвертер. Через шар доменного чавуну продувають холодне, часто збагачене киснем повітря. Протікає екзотермічна реакція утворення газоподібних (CO2, SO2) та інших оксидів (SiO2, P4O10), останні зв’язуються в фосфати і силікати за допомогою основної футеровки (доломіту):
6CaO + P4O10 = 2Ca3(PO4)2
2CaO + SiO2 = Ca2SiO4
Добутий шлак (томасшлак) подрібнюють і використовують як фосфорні добрива (томасове борошно).
В результаті конвертації вміст карбону в сплаві знижується в більшому ступені, ніж це необхідно для отримання технічно якісних сталей, тому перед спуском розплаву з конвертера в нього додають розраховану (на основі хімічного аналізу проби розплаву) кількість багатого карбоном дзеркального чавуну (фероманган).
За видозміненим способом (відомим з 1951 року) конвертерну переробку будь-якого чавуну в сталь здійснюють за допомогою чисто кисневого продування (а не повітряного) під надлишковим тиском 0,7 – 1,0 МПа. При використанні кисневого продування, якість сталі не погіршується внаслідок впливу азоту повітря (при повітряному продуванні). До переваг кисневого продування відносяться також досягнення більш високої температури (вище 2000*С) і можливість використання металобрухту (до 40% маси плаву), крім того, продуктивність цього процесу набагато вищя.
Мартенівський процес (мартенівська плавка).
Процес переділу чавуну в сталь в відбивних (мартенівських) печах відомий з 1864 року. При цьому способі плавки сталі, протікають ті самі процеси, що і при бессемеровскому або томасівському конвертуванні, проте ці процеси протікають повільніше і тому їх легше контролювати і регулювати. Оскільки в мартенівських печах, на відміну від роботи конвертера, здійснюється зовнішній обігрів, то можливе отримання сталі з сировини з більшими добавками сталевого брухту (скрап) і відпадає необхідність зворотного додавання карбону після закінчення процесу плавки.
У мартенівській печі суміш сирого чавуну і скрапу, що знаходиться на плоскому поду, розплавляється полум’ям попередньо підігрітих газів, які згоряють в суміші з повітрям (вони нагріваються газами процесу в регенеративній топці). Під дією основних флюсів (вапняк, доломіт, вапно) відбувається перетворення чавуну в сталь; окиснення домішок відбувається на поверхні, і повнота окиснення досягається вже через кілька годин. Шлаки мартенівського процесу (бідні на фосфор) не використовуються (йдуть у відвал).
Електроплавка. Цей вид плавки відомий з 1880 року. Проводиться в електричних дугових або індукційних печах, як сировину використовують мартенівську сталь і (або) сталевий брухт з легуючими добавками (нікол, ферохром, феррованадій і ін.), Для продувки розплаву використовують чистий кисень (азот повітря погіршує якість сталі). Продукт електроплавки – високоякісні леговані сталі різного призначення.
Електронно-променева плавка. Цим способом отримують особливо чисту сталь. Плавку проводять в високовакуумних печах (0,133 Па). Злитки або пресовані бруски сировини розплавляються (за рахунок перетворення кінетичної енергії потоку електронів в теплову енергію при ударі об поверхню матеріалу). Переплавлений рафінований продукт розливається мідні кокілі (ливарні форми), які охолоджуються водою. Отримана сталь майже не містить пов’язаних газів і шлаків.
Термічна обробка сталі. Існує кілька видів термічної обробки, які проводять з метою зміни структури сплавів і, отже, для набуття ними необхідних фізико-хімічних і механічних властивостей:
- випал – для зменшення внутрішньої напруги і гомогенізації структури;
- гартування – для підвищення твердості, зносостійкості при терті; проводиться шляхом занурення в воду або масло, еластичність і гнучкість при гартуванні сталі знижуються; температура нагрівання та охолодження, а також швидкість охолодження визначають властивості загартованої сталі;
- відпустк – для зниження твердості і крихкості, збільшення еластичності і ковкості; проводиться після гарту шляхом витримування загартованої сталі при 200 – 300*С (точне значення визначається з появою кольорів мінливості);
- поліпшення – для збільшення здатності до деформації розтягування і твердості; проводиться загартуванням і відпустком при відносно високій температурі (450 – 700*С); в основному цей процес використовується для обробки нелегованих і низьколегованих сталей;
- цементація – для затвердіння поверхні (при хорошій в’язкості всього матеріалу); проводиться шляхом багатогодинного (2-8 годин) випалу із застосуванням надлишку карбону у формі, наприклад суміші деревного вугілля і барій карбонату; при цьому поверхня сталі насичується карбоном (утворюється поверхневий цементит); в основному цей процес використовується для обробки нелегованих і низьколегованих сталей з вмістом карбону менше 0,2%;
азотування – для підвищення твердості поверхні; проводиться шляхом нагрівання сталі в атмосфері амоніаку при 500*С, при цьому на поверхні сплаву утворюється твердий ферум нітрид.