Черная металлургия
Черная металлургия – отрасль тяжелой промышленности по производству чугуна, стали, проката, ферросплавов, а также стальных и чугунных изделий.
Схема организации металлургических производств.
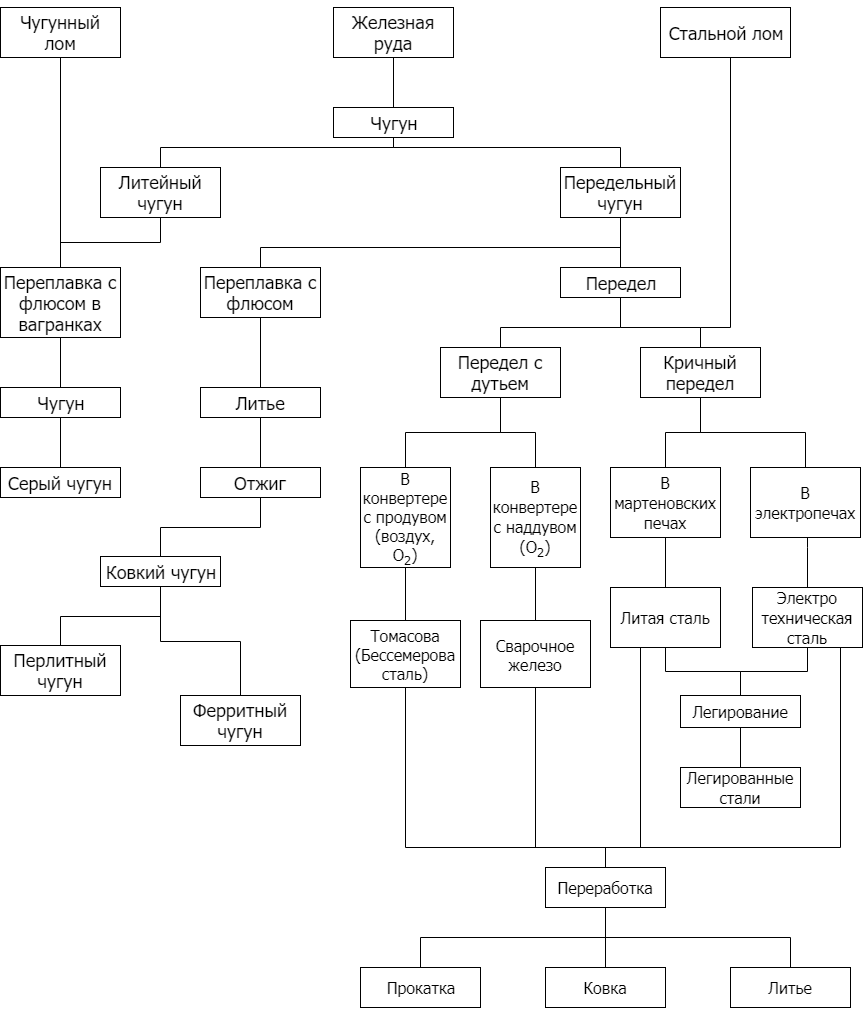
Производство чугуна
Подготовка руды включает следующие процессы:
- Обогащение основным веществом сухим, мокрым или магнитным способом;
- Перевод неоксидных руд методом обжига в оксиды, например, для пирита FeS2 и сидерита FeCO3:
4FeS2 + 11O2 = 2Fe2O3 + 8SO2
6FeCO3 + O2 = 2(FeIIFeIII2)O4 + 6CO2
- Создание необходимого гранулометрического состава путем измельчения или брикетирования.
Способы плавки чугуна:
- доменный процесс (получение всех видов чугуна);
- процесс во вращающихся трубчатых печах (получение только передельного чугуна).
Доменный процесс складывается из следующих стадий:
- Противоток – твердая шихта продвигается по доменной печи сверху вниз, а газы, наоборот, снизу вверх;
- Образование монооксида углерода – горячий воздух (“горячее дутье”) при 800*С, получаемый в доменных воздухонагревателях (кауперы), обогащается кислородом и через фурмы вдувается в домну, в этом воздухе происходит неполное сгорание кокса (так как кокс берут в избытке) с образованием монооксида углерода CO, который поднимается вверх;
- Восстановление железной руды – происходит под действием монооксида углерода (непрямое восстановление) и тонкоизмельченного кокса (прямое восстановление), при этом образуется твердое губчатое железо;
- Регенерация монооксида углерода – образовавшийся при восстановлении железной руды диоксид углерода переводится коксом снова в CO, который возвращается на стадию восстановления железной руды;
- Науглероживание железа – губчатое железо катализирует процесс .установления равновесия (равновесие Будуара):
2CO ⇄ CO2 + C
тонкодисперсный уголь проникает в железо и понижает температуру плавления железа до 1150*С, т. е. приблизительно на 400*C;
- Расплавление и спуск чугуна – при температуре выше 1150*С сплав железа с углеродом плавится, расплав собирается в металлоприемке (горн), откуда периодически (каждые 4-6 часов) осуществляется его спуск;
7. Образование и спуск шлака – шлак образуется в расплавленной зоне из присутствующих в руде примесей и флюсов, последние переводят тугоплавкие компоненты руды в легкоплавкий шлак. К кислым рудам (богатые SiO2) добавляют основные флюсы (CaCO3), а в основные руды (богатые CaCO3) вводят кислые флюсы (SiO2). Порода с флюсами и глиной образует шлак, состоящий из алюмосиликатов кальция. Шлак собирается на поверхности расплава чугуна, спуск шлака осуществляют либо периодически, либо непрерывно.
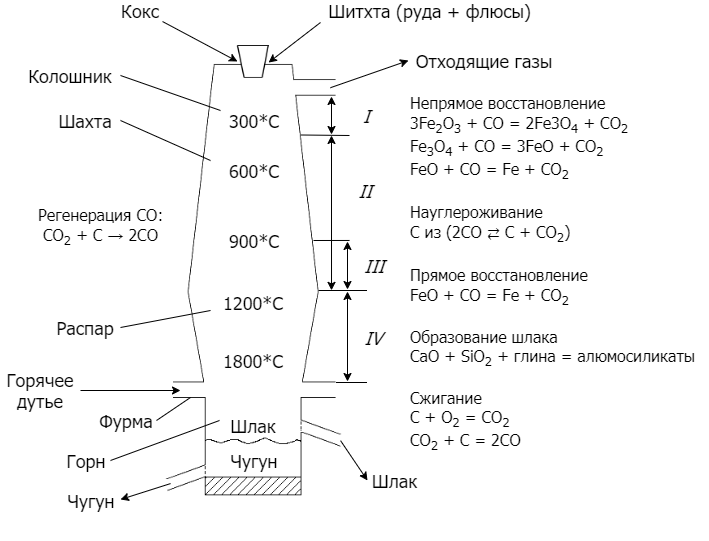
Принципиальная схема доменной печи и процессы, протекающие при выплавке чугуна. I – зона предварительного подогрева; II – зона восстановления; III – зона науглероживания; IV – зона плавления.
Продукты доменного процесса:
- чугун, содержащий, кроме Fe, 3-5% C, 0,3 – 2,5% Si, 0,5 – 6,0% Mn, 0,08 – 2,2% P и 0,03 – 0,12% S;
- доменный шлак, состоящий из алюмосиликата кальция. Используют для приготовления щебня, гравия, шлакобетона, термозита (шлаковая пемза), пенобетона, шлаковаты (для термоизоляции), быстро охлажденный и перемолотый шлак идет на получение доменного портландцемента;
- доменный газ, содержащий 60% N2, 30% CO, 10% CO2 и много пыли. После удаления пыли этот газ используют для подогрева воздуха, для выработки электроэнергии (на ТЭЦ) и как горючий газ.
Процесс получения чугуна во вращающихся трубчатых печах заключается в смешивании измельченной руды с угольной пылью и нагревании этой смеси путем сжигания части угольной пыли. В этом процессе образуются бедные по содержанию углерода гранулы чугуна, которые перерабатывают в сталь.
Отжиг чугуна – термическая обработка сырого чугуна с целью улучшения ковкости, в результате получают ковкий перлитный и ковкий ферритный чугун.
Чтобы получить перлитный чугун, сырой чугун разливают в формы, полученные слитки уплотняют смесью Fe2O3 и (FeIIFeIII2)O4 в течение пяти-шести дней выдерживают при 950 – 1000*С, при этом поверхность слитка обезуглероживается и чугун становится похожим по ковкости на сталь. Его применяют для изготовления небольших предметов (ключей, деталей замков, рычагов, звеньев цепей, гаек и т.п.).
Чтобы получить ферритный чугун, проводят отжиг сырого чугуна, покрытого слоем песка и шлака, в течение трех-четырех дней, при этом избыточный углерод выделяется из чугуна в виде графита и чугун становится ковким.
Производство стали
Конвертерный и мартеновский процессы (бессемеровская плавка и томасовская плавка).
Передел чугуна в сталь основан на удалении из него S, P и Si, а также снижении содержания углерода посредством окисления.
Способ передела чугуна в конвертере был открыт в 1854 году (Бессемер, Англия). Этот сиособ пригоден только для передела чугунов, бедных на фосфор. Передел чугунов со значительным содержанием фосфора стал возможным только после разработки в 1878 году (Томас, Англия) процесса с использованием конвертера с футеровкой материалами, которые обладают основными свойствами.
Конвертерный процесс.
Передел чугуна проводят в специальном аппарате – конвертер. Через слой доменного чугуна продувают холодный, часто обогащенный кислородом воздух. Протекает экзотермическая реакция образования газообразных (CO2, SO2) и других оксидов (SiO2, P4O10), последние связываются в фосфаты и силикаты с помощью основной футеровки (доломита):
6CaO + P4O10 = 2Ca3(PO4)2
2CaO + SiO2 = Ca2SiO4
Получающийся шлак (томасшлак) измельчают и используют в качестве фосфорного удобрения (томасова мука).
В результате конвертирования содержание углерода в сплаве снижается в большей степени, чем это необходимо для получения технически качественных сталей, поэтому перед спуском расплава из конвертера в него добавляют рассчитанное (на основе химического анализа пробы расплава) количество богатого углеродом зеркального чугуна (ферромарганец).
По видоизмененному способу (известному с 1951 года) конвертерную переработку любого чугуна в сталь осуществляют с помощью чисто кислородного дутья (а не воздушного) под избыточным давлением 0,7 – 1,0 МПа. При таком способе предотвращается ухудшение качества стали, вызываемое азотом воздуха (при воздушном дутье). К преимуществам кислородного дутья относятся также достижение более высокой температуры (выше 2000*С) и возможность использования металлолома (до 40% массы плава), кроме того, производительность этого процесса намного выше.
Мартеновский процесс (мартеновская плавка).
Процесс передела чугуна в сталь в отражательных (мартеновских) печах известен с 1864 года. При этом способе плавки стали, протекают те же процессы, что и при бессемеровском или томасовском конвертировании, однако эти процессы протекают медленнее и поэтому их легче контролировать и регулировать. Поскольку в мартеновских печах, в отличие от работы конвертера, осуществляется внешний обогрев, то возможно получение стали из сырья с большими добавками стального лома (скрап) и отпадает необходимость обратного науглероживания по окончании процесса плавки.
В мартеновской печи смесь сырого чугуна и скрапа, находящаяся на плоском поду, расплавляется пламенем предварительно подогретых сгорающих газов в смеси с воздухом (они нагреваются отходящими газами процесса в регенеративной топке). Под действием добавляемых основных флюсов (известняк, доломит, известь) происходит передел чугуна в сталь; окисление примесей происходит на поверхности, и полнота окисления достигается уже через несколько часов. Шлаки мартеновского процесса (бедные на фосфор) не используются (идут в отвал).
Электроплавка. Этот вид плавки известен с 1880 года. Проводится в электрических дуговых или индукционных печах, сырьем служат мартеновская сталь и (или) стальной лом с легирующими добавками (никель, феррохром, феррованадий и др.), для продувки расплава используют чистый кислород (азот воздуха ухудшает качество стали). Продукт электроплавки – высококачественные легированные стали различного назначения.
Электроннолучевая плавка. Этим способом получают особо чистую сталь. Плавку проводят в высоковакуумных печах (0,133 Па). Слитки или прессованные бруски сырья расплавляются (за счет превращения кинетической энергии потока электронов в тепловую энергию при ударе о поверхность материала). Переплавленный рафинированный продукт разливается в охлаждаемые водой медные кокили (литейные формы). Полученная сталь почти не содержит связанных газов и включений шлаков.
Термическая обработка стали. Существует несколько видов термической обработки, которые проводят с целью изменения структуры сплавов и, следовательно, для придания им необходимых физико-химических и механических свойств:
- отжиг – для уменьшения внутренних напряжений и гомогенизации структуры;
- закалка – для повышения твердости, износостойкости при трении; проводится путем погружения в воду или масло, эластичность и ковкость при этой обработке снижаются; температура нагревания и охлаждения, а также скорость охлаждения определяют свойства закаленной стали;
- отпуск – для снижения твердости и хрупкости, увеличения эластичности и ковкости; проводится после закалки путем выдерживания закаленной стали при 200 – 300*С (точное значение определяется по появлению цветов побежалости);
- улучшение – для увеличения способности к деформации растяжения и твердости; проводится закалкой и отпуском при относительно высокой температуре (450 – 700*С); в основном этот процесс используется для обработки нелегированных и низколегированных сталей;
- цементация – для отверждения поверхности (при хорошей вязкости всего материала); проводится путем многочасового (2-8 часов) отжига с применением избытка углерода, например смеси древесного угля и карбоната бария; при этом поверхность стали науглероживается (образуется поверхностный цементит); в основном этот процесс используется для обработки нелегированных и низколегированных сталей с содержанием углерода менее 0,2%;
азотирование – для повышения твердости поверхности; проводится путем нагревания стали в атмосфере аммиака при 500*С, при этом на поверхности сплава образуется твердый нитрид железа.